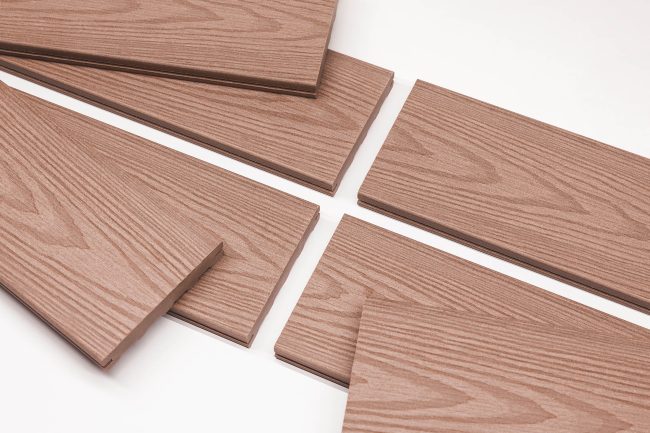
60 % wood
The hardness and/or origin of the wood have no effect on the quality. In America, the boards are manufactured even from rice, grain or paper. What matters the most is the length and thickness of the fibre.
30 % plastic
Several types of plastic are used, each one of them with different features. The cheaper plastics (such as polypropylene) get brittle in freezing temperatures, whereas HDPE and PVC are the best quality materials for the making of wood-plastic.
Quality products contain about 10 % of silicone, UV stabilizers, colouring agents and adhesives.
Although it is only a small proportion, it is the most important and expensive item. In addition, each company has its own production method and proportion of ingredients – and these few per cent become a protected know-how. If the company decided to save on costs of any of these items, the boards would disintegrate and the material would deteriorate in a short time.